Importance of Regular Laser Machine Maintenance
Maintaining laser machines is crucial in ensuring their optimal performance and longevity, especially in high-quality, wholesale production environments. Without routine upkeep, these machines could face increased downtime, leading to potential losses for factories. Regular maintenance not only enhances machine efficiency but also reduces the risk of expensive repairs.
Financial Implications of Neglected Maintenance
Studies have shown that neglecting laser machine maintenance can result in repair costs up to three times higher than what would typically be spent on regular upkeep. For instance, dealing with issues like malfunctioning laser outputs or misaligned components can interrupt production lines, causing significant financial strain.
Daily Maintenance Checks for Laser Systems
Daily checks form the foundation of a comprehensive maintenance strategy. These routines help prevent minor issues from escalating into major operational disruptions.
Routine Cleaning and Inspection
Daily cleaning tasks involve removing dust and debris from both the interior and exterior parts of the machine. It is imperative to check the machine bed and its x, y, and z axes for wear or damage to ensure smooth operation.
Operational Parameter Verification
Checking the machine's alignment settings and recalibrating them as necessary is vital. Ensuring the laser working gas pressure and limit switches' sensitivity are correctly set helps maintain precision in operations.
Weekly Maintenance Tasks for Optimal Performance
Weekly maintenance tasks are more detailed than daily checks and aim to sustain high-quality output in a wholesale production environment.
Fluid Levels and Calibration Checks
Weekly routines involve verifying fluid levels, such as coolant and lubricants, essential for machine operation. Ensuring that all sensors and measurement systems are correctly calibrated is crucial to prevent delays and quality issues.
Lubrication and Component Checks
Regular lubrication of moving parts and inspections of belts, motors, and bearings help in avoiding unexpected breakdowns. Replacing worn-out components as needed ensures the machine's continued high performance.
Monthly Inspection for Comprehensive Health Assessment
Monthly inspections are necessary for a thorough evaluation of the machine's condition, focusing on parts that are prone to wear over time.
Laser Source and System Stability
Evaluating the stability and performance of the laser source helps in maintaining the machine's cutting or engraving efficiency. Regular checks on fiber laser sources are paramount to sustaining production quality.
Software and Firmware Updates
Monthly reviews should include updating software and firmware to incorporate the latest optimizations and security upgrades, extending the machine's productive life.
Recognizing Signs of Wear and Tear
Being aware of signs that indicate potential problems is key to effective maintenance.
Indicators of Component Deterioration
Common signs of wear include contamination of optics and poor focusing, which may result in compromised product quality. Failure to maintain proper temperatures can lead to overheating, risking laser failure.
Preventive Maintenance Strategies
Preventive maintenance is central to avoiding major repairs and ensuring smooth operations in a factory setting.
Scheduled Routines and Key Focus Areas
- Regularly replace chiller water every six months.
- Lubricate the y-axis linear guide bearings to prevent mechanical failures.
- Oil the x-axis rail guides to ensure precision.
Causes and Solutions for Common Laser System Failures
Identifying the root causes of systemic failures aids in implementing effective solutions.
Major Causes of System Failures
Misalignment, dirt on optics, and neglected cooling systems are primary reasons for laser system malfunctions. These issues reduce beam intensity and lead to overheating, severely affecting the machine's lifespan.
Implementing Practical Solutions
Regular external cleaning to remove dust is crucial. Ensuring the cooling system is functioning correctly by changing coolant at prescribed intervals prevents overheating and system degradation.
Role of Technological Advancements in Maintenance
Technological improvements can simplify and enhance maintenance processes in factories.
Innovation in Maintenance Tools and Techniques
Advanced calibration tools and automated diagnostic systems help in identifying and rectifying issues promptly. These technologies ensure that laser machines operate at peak efficiency, especially in a high-quality production environment.
Environmental and Safety Considerations
Maintaining laser machines also involves adhering to environmental and safety standards, which are increasingly crucial in factory settings.
Regulatory Compliance and Workplace Safety
Using environmentally friendly coolants and ensuring proper waste disposal are essential practices. Regular checks for safety compliance help in creating a secure working environment.
Return on Investment Through Maintenance Practices
Efficient maintenance practices contribute significantly to the financial health of a factory.
Maximizing Equipment Lifespan
Consistent maintenance extends equipment life, providing a better return on investment. Many factories report that their systems pay for themselves within 12-24 months through direct cost savings and enhanced productivity.
Langsheng Laser Provide Solutions
Langsheng Laser offers extensive solutions tailored to maintain high-quality laser systems in wholesale production environments. Our services include comprehensive maintenance plans that cover daily, weekly, and monthly tasks, ensuring your machines remain in peak condition. By partnering with Langsheng Laser, you benefit from our expertise in prolonging machine life, reducing downtime, and maintaining operational excellence. Our team can assist you in implementing preventive and corrective measures, optimizing your factory's production capabilities.
User hot search: new laser machine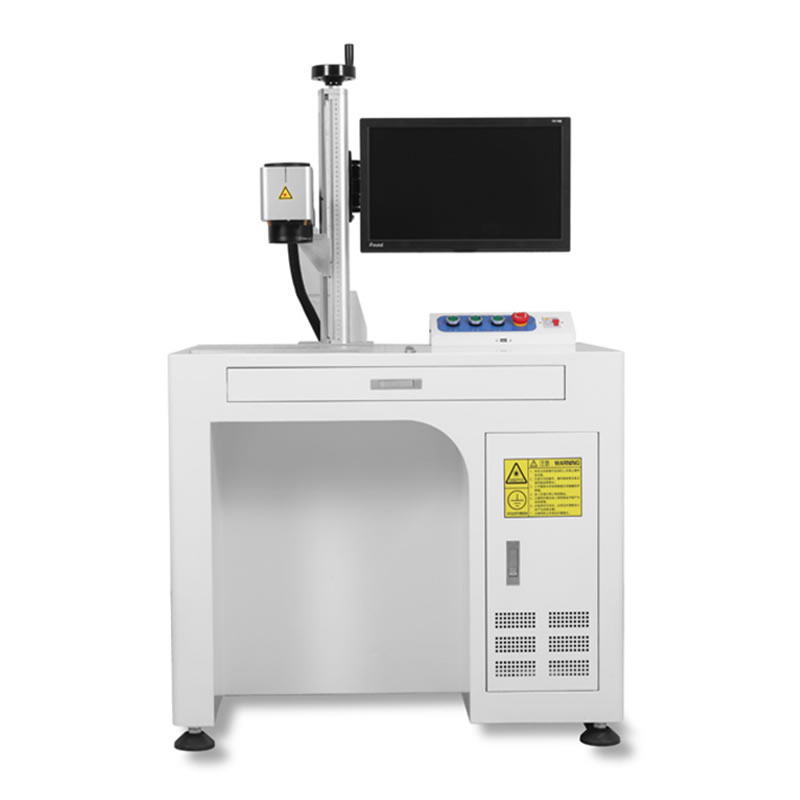
Post time: 2025-06-16 10:36:07